Tel: +1 952 8950200
Fax: +1 952 8956020
info@formacoat.com
Incorporated in 2002, Formacoat is located in the southwest suburbs of Minneapolis, MN. Our roots come from the diverse community of Twin Cities companies that have made our area a world center for the medical device and life science industries. Their brand new 38,000 square foot facility, with 3 - Level 7 clean rooms totalling 8,400 square feet of Cleanroom space, combined with a catalogue of over 90 different types of coatings from 45 different vendors all over the world, Formacoat stands at the ready to take our customer’s concept to cash flow!
As a uniquely positioned medical device coating services contract manufacturer, Formacoat is dedicated to providing value to its customers around the world by improving the design, functionality and performance of their clients’ medical devices. They work expertly with their customers to improve medical device functionality and performance.
Through aligned objectives and collaborative efforts, Formacoat makes the tools of medicine run smoother.Formaocat are THE specialists in providing coating-engineered application solutions utilized in sophisticated medical device design and development for scalable, dependable production.In their offerings from different coating vendors, they have a variety of different technologies to choose from which include Hydrophilic, Hydrophobic, Surface-blocking and Anti-fouling, Anti-Microbial, Heparin, Collagen and PSA/Adhesive.They have thermal cure, UV cure and grafting coating technologies as well. And with their vast array of equipment and technology, they are the experts in our field when it comes to coating Stents, Catheters, Guidewires, Mesh and Films.
You name it, Formacoat can coat it!
We Collaborate with Different Coatings Vendors to Bring Your Custom Coating Solutions to Life
There is no one “best” medical device coating. Some are really good in some situations, and not so in others. Some may work better than one situation needs, and end up costing that way too. Medical device performance requirements have become progressively more demanding over time. Formacoat works with over 40 different coating formulators who offer over 80 different coating chemistries and technologies. We use these different technologies to address the specific needs and challenges of each device in creative, robust and cost efficient ways. Formacoat’s expertise provides a powerful partner in this niche area of medical device coatings.
In our offerings from different coating vendors, we have a variety of different technologies to choose from which include Hydrophilic, hydrophobic, Surface-blocking and Anti-fouling, Anti-Microbial, Heparin, Collagen and PSA/Adhesive coatings. We have thermal cure, UV cure and grafting technologies as well. By working with Formacoat, our knowledge of your device and needs gathers momentum if first options don’t work as well as expected, rather than you having to start all over with another vendor. When starting out with initial comparative studies, we can do comparison friction testing to augment your own functional testing.
Why Medical Device Manufacturers Partner with Us
Experience True Service with Our Value-Added Focus!
Device manufacturers working with Formacoat cover a cross-section of application types, designs, company sizes and geographic locations including:
Vascular and cardiovascular, auditory, ophthalmic, implant delivery
Catheters, guidewires, tubing, wire, roll to roll applications, film, screen
Medical businesses, and unique industrial applications
Fortune 500 companies, mid-sized companies and small start-ups
U.S. and Internationally-based companies
Our customers value the collaborative input and experience of Formacoat staff and the way they relate to designing a repeatable, scalable coating process. Even better, they enjoy working with us and appreciate the personal relationships we foster!
In addition, Formacoat can provide guidance on regulatory compliance with its staff seasoned in medical device development and compliance expertise. Each partner’s needs are unique, and Formacoat’s response to those needs is unique as well.
Formacoat’s satisfaction comes when customers gain an edge over the past performance of their medical devices as a result of working together with us. As demand for lubricious hydrophilic coated devices and specialized hydrophobic coatings has grown, Formacoat has grown as well, with classic “Win-Win” client relationships.Whether your requirements are to coat inner/outer diameters or complex part shapes, click here to learn more about Formacoat’s medical device and substrate coating capabilities.
Formacoat's experience includes coating the inner and outer diameters, or the complex component shapes, of the following medical device types withanti-microbial properties, among others:
- Films
- Micro-Catheters
- Drug Delivery Catheters
- Stent Delivery-System Catheters
- Embolic Capture Devices
- Medical Device Balloons
- Component Level Materials
- Hypo Tubes
- Micro-well plates
- IVD
- IOL Insertion Cartridges and other ophthalmic devices
- Medical device Implants
- And much, much more!
In addition, Formacoat can provide guidance on regulatory compliance with its staff seasoned in medical device development and compliance expertise. Each partner’s needs are unique, and Formacoat’s response to those needs is unique as well.Formacoat’s satisfaction comes when customers gain an edge over the past performance of their medical devices as a result of working together with us.
As demand for lubricious hydrophilic coated devices and specialized hydrophobic coatings has grown, Formacoat has grown as well, with classic “Win-Win” client relationships.Formacoat is family owned and its second generation members are invested in maintaining the quality and consistency that comes from sustaining long term relationships with employees, customers and vendors. Formacoat's family owners are committed only to the success of the business, without the short-term monetary pressure and the sudden upsets in culture that often comes with private equity and venture capital types of ownerships. This means that the Formacoat family will continue to work for you, providing the coating expertise you need.Whether your requirements are to coat inner/outer diameters or complex part shapes, click here to learn more about Formacoat’s medical
Contact Formacoat
Questions & Inquiries
Mark and the Formacoat biomedical coating services team welcome your inquiry. Please contact us at:
Formacoat
2960 Chaska Blvd
Chaska, MN 55318, USA
Tel: 952.895.0200
Fax: 952.895.6020
Email: info@formacoat.com

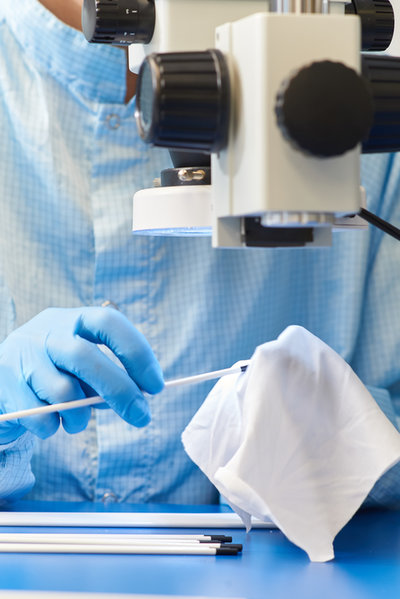
Our Hydrophilic and Hydrophobic Coatings Technologies and Vendors
The Formacoat Formula
What do you want and why? While this may seem like a basic concept, it is one that often times can be overly complicated and even missed altogether. We’re continually amazed at how important the answers are to those seemingly simple questions. Before we offer answers to your coating challenges, we want to know what you care about, even what the customer who use your device care about. By digging deeper and listening to our customer’s needs, we gain a better understanding of what you need that leads to improved results, sooner.
Another favorite formula: Medical device design insight yields manufacturing lubricious coatings foresight.
With the expansion of their new facility and greatly expanded production floor, Formacoat has invested a large amount of time, energy and resources necessary for getting into the drug coating market. Their coating capabilities now include drug coatings (DES, Drug Eluting Stents) for coronary, peripheral stents, neuro devices and balloon catheters as well as the contract manufacturing service applied to those devices.
They offer coatings from the full range of polymeric materials and chemistries for specific customer needs and indications with many ways to apply coatings to different kinds of devices, substrates and materials - and the commercial scale equipment to do so at any level of production.One of their newest vendor offerings, a grafting technology, has been in commercial development at Formacoat for the last couple of years. This revolutionary technology allows them to graft to select substrates in such a fashion that it creates a durable, lubricious layer that is tunable for our customer’s specific requirements.
Imagine this coating like a field of grass; they can configure the parameters is such a fashion that we can not only have the grass sprout up wherever they would like but also as thick or thin as possible. This allows them to tune the lubricity and durability and is excellent for the smallest of IDs where traditional hydrophilic coatings are unable to be functionally applied. As this is chemically grafted to the substrate of your device, it also allows for excellent flexibility with our fear of the coating cracking or de-laminating. This process can offer pricing that is lower than other coatings.